Predicting the Future of Supply Chains: Learning from the Past to Navigate Uncertainty

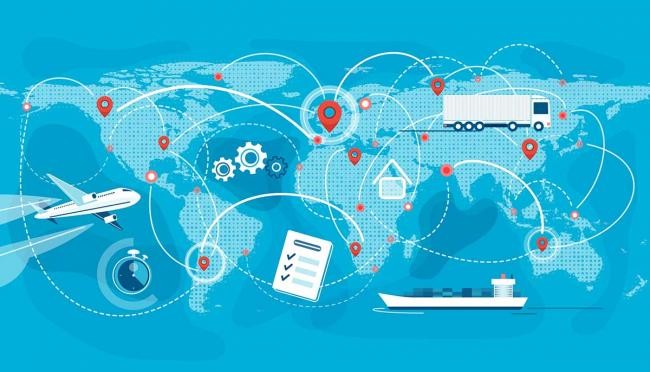
by Chris Gaffney, Georgia Tech Supply Chain & Logistics Institute
Predicting the future of supply chains has always been a challenging endeavor. As someone who has spent more than 25 years in the beverage industry, I’ve witnessed firsthand how even the most well thought out predictions can miss the mark. Yet, understanding where we went wrong in the past can equip us with the tools to better anticipate and adapt to future challenges.
In this article, I want to explore the complexities of forecasting in the supply chain realm, reflect on some past predictions that didn’t quite hit the target, and suggest actionable strategies that can help us navigate the uncertainties ahead.
The supply chain, particularly in the beverage industry, is a complex web of interdependencies. As we push for innovation—from new ingredients to advanced packaging—our supply chains often struggle to keep pace. Historically, the challenges of maintaining quality, managing costs, and ensuring timely delivery have been compounded by global disruptions, technological advancements, and evolving consumer expectations.
In the 1990s, for example, the advent of RFID technology was hailed as a gamechanger, promising unparalleled visibility and efficiency. While RFID has undoubtedly transformed many aspects of supply chain management, its adoption has been slower and less impactful than originally anticipated. Similarly, the introduction of Enterprise Resource Planning (ERP) systems was expected to revolutionize the way businesses managed their operations. Yet, the promised seamless integration and real time data accuracy have often fallen short, leading to frustrations and costly implementations.
These examples highlight a critical lesson: while technological advancements hold great promise, their real-world application can be fraught with challenges that delay or dilute their impact.
One of the most striking examples of a prediction that didn’t pan out as expected is the Just in Time (JIT) manufacturing model. Initially, JIT was celebrated for its potential to minimize waste and reduce inventory costs. However, the COVID-19 pandemic exposed the vulnerabilities of this approach. As supply chains were disrupted worldwide, many companies found themselves unable to meet demand due to the lack of buffer stock. This has led to a reevaluation of the JIT model, with many businesses now looking to build more resilience into their supply chains by maintaining higher levels of inventory.
Another lesson comes from the early 2000s, when global sourcing was predicted to be the ultimate cost saving strategy. While it did lead to significant cost reductions, it also introduced new risks—ranging from quality control issues to geopolitical tensions—that have since prompted companies to reconsider the balance between cost savings and supply chain security.
One of the inherent risks in predicting supply chain trends is that it often leads to an overreliance on certain strategies or technologies. For instance, the push towards automation and robotics, while offering substantial benefits in terms of efficiency and cost savings, has also led to significant challenges. The initial costs, integration difficulties, and the need for upskilling workers have often been underestimated, leading to delays and unfulfilled promises.
Moreover, as we’ve seen with technologies like blockchain and AI, the hype often outpaces the reality. While these technologies have immense potential to transform supply chain management, their implementation has been slower and more complex than initially expected. This lag can create a false sense of security, leading companies to delay the adoption of alternative strategies or to underinvest in more immediately impactful areas.
Given the inherent challenges of predicting the future, how can companies better prepare for what lies ahead? Here are a few strategies that can help:
- Embrace Flexibility and Resilience: Instead of betting on a single prediction or technology, companies should build flexibility into their supply chains. This might involve diversifying suppliers, maintaining higher inventory levels, or investing in modular production systems that can be quickly adapted to changing circumstances.
- Invest in Predictive Analytics: While past predictions have often fallen short, advances in AI and machine learning are making it possible to better anticipate supply chain disruptions and demand fluctuations. By investing in predictive analytics, companies can gain more accurate insights into future trends and make more informed decisions.
- Foster Stronger Relationships with Partners: As supply chains become more complex and globalized, the importance of strong relationships with suppliers and partners cannot be overstated. By working closely with partners, companies can ensure better alignment of goals, improved quality control, and more effective collaboration in the face of disruptions.
- Prioritize Sustainability: As consumer expectations shift towards more sustainable products, companies that prioritize sustainability in their supply chains will be better positioned to meet future demand. This might involve investing in sustainable sourcing practices, reducing waste, or adopting circular economy principles.
- Continual Learning and Adaptation: Finally, companies should foster a culture of continual learning and adaptation. By staying informed about the latest trends, technologies, and best practices, businesses can more effectively navigate the uncertainties of the future and seize new opportunities as they arise.
Predicting the future of supply chains is a daunting task, but it’s one that we must continually strive to master. By learning from past mistakes and adopting a proactive, flexible approach, we can better navigate the challenges ahead and turn potential disruptions into opportunities for growth and innovation. As we look to the future, let’s remember that while predictions can guide us, it’s our ability to adapt and respond to the unexpected that will ultimately determine our success.
The Georgia Tech Supply Chain and Logistics Institute (SCL) is the largest supply chain and logistics leadership institute in the world providing comprehensive research, education, and outreach programs. For more than thirty years, SCL has been a world leader across a broad range of supply chain and logistics domains. SCL provides global leadership for interdisciplinary research and education in the application of scientific principles to frame and optimize the design and management of supply chains and logistic systems; the integration of supply chain and logistic strategy, infrastructure, processes, and technology; and to conceptualize and roadmap pathways toward next-generation supply chain and logistics ecosystems.
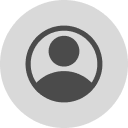