Baltimore Bridge Collapse: An Opportunity to Reinforce the Importance of Supply Chain Resilience

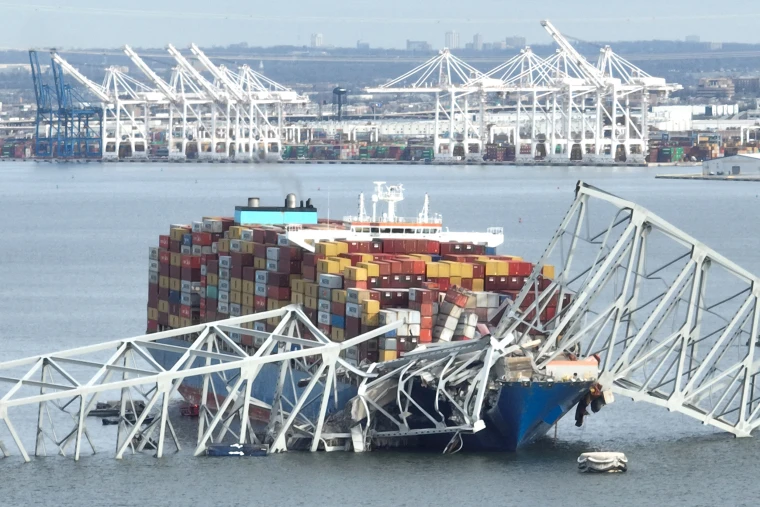
By Alex Chatha, Logistics Viewpoints
Supply chain resilience is a hot topic the last few years since post-Covid issues and newsworthy incidents like the Houthi attacks in the red sea have raised awareness. The Francis Scott Key Bridge in Baltimore being struck by the Dali and collapsing is an unpredictable disruption to the supply chains of several industries including automobiles, coal, and agricultural machinery. Baltimore is one of the busiest ports on the east coast, and the bridge collapse was not only a tragedy, but a reminder that supply networks remain fragile and disruptions are not always anticipated.
The bridge collapse is a stark reminder of the vulnerability of the nation’s aging infrastructure and the importance of supply chain resilience. Supply chain resilience is the ability of a supply chain to withstand and recover from disruptions, such as natural disasters, accidents, cyberattacks, or pandemics. A resilient supply chain can maintain its functionality and performance, minimize losses, and adapt to changing conditions. Supply chain resilience is crucial for ensuring the continuity of business operations, the delivery of essential goods and services, and the protection of public safety and national security.
The collapse had several immediate and long-term consequences for the region. The most obvious impact was the disruption of traffic and transportation. The bridge was a vital link for commuters, tourists, and truck drivers, who had to find alternative routes or modes of travel. The bridge also carried several utility lines, such as water, gas, and fiber optic cables, which were severed or damaged by the collapse. The bridge’s closure also affected the operations of the Port of Baltimore, which is one of the busiest and most important ports on the East Coast. The port handles about 11 million tons of cargo per year, including automobiles, containers, coal, and farm products. The port relies on the bridge to connect the rail network and the interstate highway system, which are essential for moving goods to and from the port. The port’s closure could have significant economic and environmental impacts, as well as implications for national security and defense. The neighboring port in Norfolk Virginia and other east coast ports like New York City can absorb the additional traffic without many complications or delays, but this incident provides an opportunity to discuss the importance of supply chain resilience.
Supply Chain Resilience: Concept and Dimensions
Supply chain resilience is a multidimensional concept that encompasses various aspects of a supply chain’s ability to cope with disruptions. According to a widely cited framework by Christopher and Peck from “Building the Resilient Supply Chain” (2004), supply chain resilience consists of four dimensions: robustness, agility, redundancy, and flexibility. These dimensions are briefly defined and illustrated below.
Robustness is the ability of a supply chain to resist disruptions and maintain its normal operations. A robust supply chain has strong and reliable components, such as infrastructure, equipment, technology, and human resources, that can withstand shocks and stresses. For example, a robust supply chain may have backup power generators, firewalls, security systems, and emergency plans to prevent or mitigate the effects of disruptions.
Agility is the ability of a supply chain to respond quickly and effectively to disruptions and restore its functionality and performance. An agile supply chain has dynamic and adaptive capabilities, such as information, communication, coordination, and collaboration, that enable it to sense, analyze, and act on disruptions. For example, an agile supply chain may have real-time data, advanced analytics, decision support tools, and cross-functional teams to monitor, diagnose, and solve problems.
Redundancy is the ability of a supply chain to have extra or alternative resources and options to cope with disruptions. A redundant supply chain has spare or backup capacity, such as inventory, equipment, facilities, and suppliers, that can be activated or mobilized in case of disruptions. For example, a redundant supply chain may have safety stocks, contingency contracts, multiple sourcing, and diversified networks to ensure the availability and continuity of supply.
Flexibility is the ability of a supply chain to adjust or change its structure, processes, or products to cope with disruptions. A flexible supply chain has versatile and modular capabilities, such as design, production, distribution, and service, that enable it to adapt to changing customer needs, market conditions, or environmental factors. For example, a flexible supply chain may have product customization, mass customization, postponement, and reconfiguration to meet the demand and preferences of different segments, regions, or channels.
These dimensions are not mutually exclusive or exhaustive, but rather complementary and interrelated. A resilient supply chain should have a balanced and integrated combination of these dimensions, depending on the nature, frequency, and severity of the disruptions it faces. A resilient supply chain should also have a proactive and learning orientation, meaning that it should anticipate and prepare for potential disruptions, as well as learn from and improve after experiencing disruptions.
The Impacts of the Baltimore Port Closure on Supply Chains
The closure of the Port of Baltimore due to the bridge collapse has significant impacts on the supply chains of various industries and sectors that depend on the port for importing and exporting goods. Some of the major industries and sectors that are affected by the port closure are:
Automotive industry: The Port of Baltimore is the largest auto port in the country, handling about 800,000 vehicles per year. The port serves as a gateway for importing vehicles from Europe, Asia, and South America, as well as exporting vehicles to the Middle East, Africa, and other regions. The port also handles auto parts and accessories, such as engines, transmissions, tires, and batteries. The port closure disrupts the inbound and outbound flows of vehicles and parts, affecting the operations and sales of automakers, dealers, and suppliers. The port closure also creates congestion and delays at other ports and transportation modes, such as rail and truck, that must handle the diverted cargo.
Container industry: The Port of Baltimore is the ninth-largest container port in the country, handling about 600,000 containers per year. The port serves as a hub for importing and exporting a variety of goods, such as consumer products, electronics, machinery, chemicals, and food. The port is also a major participant in the East Coast trade lane, connecting with other ports such as New York, Norfolk, Savannah, and Miami. The port closure disrupts the inbound and outbound flows of containers, affecting the operations and revenues of shippers, carriers, and terminal operators.
Coal industry: The Port of Baltimore is the largest coal port in the country, handling about 20 million tons of coal per year. The port serves as a gateway for exporting coal to Europe, Asia, and South America, as well as importing coal from Canada and Colombia. The port also handles coke, iron ore, and steel, which are related to the coal industry. The port closure disrupts the outbound flows of coal and related products, affecting the operations and profits of coal producers, exporters, and traders.
Farm industry: The Port of Baltimore is a major port for exporting farm products, such as soybeans, corn, wheat, and poultry. The port handles about 10 million tons of farm products per year, mostly to Europe, Asia, and Africa. The port also handles fertilizers, pesticides, and seeds, which are related to the farm industry. The port closure disrupts the outbound flows of farm products and related inputs, affecting the operations and incomes of farmers, exporters, and processors.
The impacts of the port closure on these and other industries and sectors are not only limited to the local or regional level, but also have ripple effects across the national and global supply chains. The port closure affects the availability, quality, and cost of goods and services, as well as the competitiveness, productivity, and innovation of businesses and industries. The port closure also affects the social and environmental aspects of supply chains, such as employment, safety, health, and sustainability. The port closure also exposes the vulnerabilities and interdependencies of supply chains, as well as the need for resilience and collaboration among supply chain stakeholders.
Best Practices and Recommendations for Enhancing Supply Chain Resilience
The Francis Scott Key Bridge collapse and the Baltimore port closure are examples of the types of disruptions that supply chains face in an increasingly complex and uncertain world. These disruptions pose significant challenges and risks for supply chain performance and survival, but also offer opportunities and incentives for supply chain improvement and innovation. To enhance supply chain resilience and cope with future disruptions, some of the best practices and recommendations are:
Assess and monitor the risks and vulnerabilities of supply chains, using tools such as risk matrices, scenario analysis, and stress testing. Identify the sources, types, and probabilities of potential disruptions, as well as their impacts and consequences for supply chain performance and objectives.
Develop and implement contingency plans and recovery strategies, using tools such as business continuity plans, crisis management teams, and emergency response protocols. Define the roles, responsibilities, and actions of supply chain stakeholders, as well as the resources, processes, and systems needed to cope with disruptions.
Build and maintain the capabilities and resources that enable supply chain resilience, using tools such as redundancy, flexibility, agility, and robustness. Invest in the infrastructure, technology, human capital, and relationships that enhance the supply chain’s ability to resist, respond, recover, and adapt to disruptions.
Learn and improve from the experiences and feedback of supply chain disruptions, using tools such as post-mortem analysis, lessons learned, and best practices. Evaluate the effectiveness and efficiency of the supply chain’s response and recovery, as well as the opportunities and challenges for improvement and innovation.
Collaborate and communicate with supply chain partners and stakeholders, using tools such as information sharing, joint planning, and coordination. Establish and maintain trust, transparency, and alignment among supply chain actors, as well as the awareness and understanding of the interdependencies and impacts of supply chain disruptions.
By following these best practices and recommendations, supply chains can enhance their resilience and cope with future disruptions. Supply chain resilience is not only a defensive and reactive capability, but also a strategic and proactive advantage. A resilient supply chain can not only survive, but also thrive, in an uncertain and dynamic world.
Alex Chatha is Director of Smart Cities, Energy, Infrastructure & Supply Chain at ARC Advisory Group