Freight Science Found New Lanes for Paper Transport Loads Two Days after Key Bridge Disaster

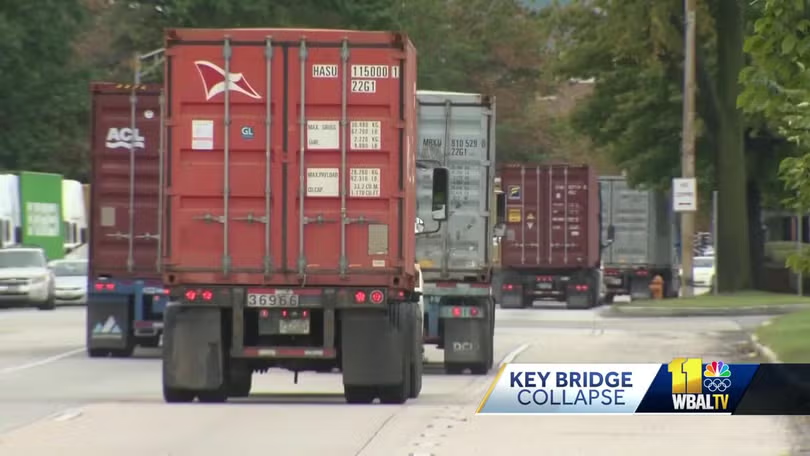
Headquartered in De Pere, Wisconsin, Paper Transport provides dedicated, over-the-road (OTR), intermodal, and brokerage solutions throughout the United States. The carrier engaged Freight Science’s load planning optimization solutions in early 2024, which immediately made a difference giving PTI a competitive advantage with its dedicated service offering. This was abundantly clear following the collapse of Baltimore’s Key Bridge in March, a vivid example of the everyday challenges that logistics and trucking industries face.
The collapse immediately changed travel time for over 70 destinations from minutes to hours, and Freight Science enabled PTI to react quickly by immediately identifying key information on all impacted and non-impacted lanes, adjusting the load planning process and resetting customer expectations.
“We were scheduled to go-live with a new dedicated account just days after the Key Bridge collapse and everyone wanted to know the impact it would have on our ability to execute,” said Matt Christianson, Director of Operations for Paper Transport. “Specifically, how many miles were going to be added, what the cost differences would be, and the overall impact on KPIs and our ability to meet them.”
“We were able to reset expectations with the customer based on real information which made them feel comfortable enough not to push the start-date out and we were able to go-live on schedule, which is huge because we already had drivers staffed, equipment positioned, and delays would have cost tens of thousands of dollars each week had we been delayed,” said Christianson.
PTI leveraged the Freight Science platform’s automated decision-making and advanced analytics, resulting in more efficient and profitable decisions to strengthen their network while building robust and scalable operations. The software has a bi-directional integration with PTI’s existing Transportation Management System (TMS), real-time electronic logging device (ELD) data, and other external data into an Artificial Intelligence model, generating an optimized load plan for the planner.
“We’ve been able to execute in the toughest of situations because we’ve got real live data of how long each event is actually going to take and a system to aid and even automate the decision making process,” said Chad Borley, Operations Manager at Paper Transport. “From what traffic patterns we are battling in the morning and evening with rush hour and things like that, to the impact of additional miles to a route, or even location-specific dwell times, it’s been a huge differentiator for us.”
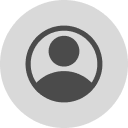