Strategies to Mitigate Supply Chain Disruption: Creating Redundancy

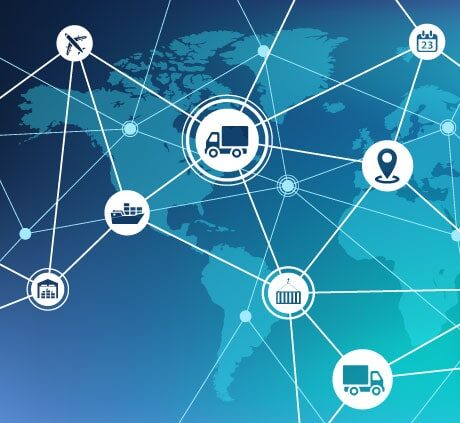
By Will Quinn, Infor
Redundancy is an important strategy to address supply chain risk. In the world of supply chain management, redundancy is not a sign of inefficiency. Instead, it’s a strategic move to ensure business continuity in the face of unexpected disruptions. The recent tsunami in Japan, which caused auto and electronics parts shortages, is a stark reminder of the importance of having redundancy in supply chains. The disruptions rippled through the global auto supply chain given Japan’s prominent role.
It’s also important to mention that redundancy and nearshoring are not mutually exclusive strategies to mitigate supply chain disruption. Many organizations find that employing both helps limit overall supply chain vulnerability. Nearshoring can bring the goods and services closer to the end customer, which can be complimented with a redundancy plan that provides multiple sources for raw materials and helps safeguard against breaks in a company’s supply chain from unforeseen events.
What is Redundancy in Supply Chain?
Redundancy in supply chain refers to the practice of having backup options or alternatives in place to ensure the continuity of supply chain operations during a supply chain crisis. This could mean having multiple suppliers for a single component, maintaining buffer inventory, or having alternative transportation routes.
Why is Redundancy Important?
Without redundancy, a single point of failure can disrupt the entire supply chain, leading to production halts, increased costs, and loss of customer trust. For example, rare earth minerals are critical for many modern technologies, including electronics, renewable energy, and defense systems. China dominates the global production and processing of rare earth minerals, accounting for over 60% of the global supply. Any disruption in China’s rare earth supply, whether due to policy changes, trade tensions, or environmental issues, can significantly impact numerous industries that rely on these specialized materials. This single-source dependence on China for rare earth minerals has led to concerns about the vulnerability of global supply chains and the need for more diversified sources of these critical resources.
Strategies for Creating Redundancy
Creating redundancy in your supply chain involves a multi-faceted approach:
- Diversification of Suppliers: Relying on a single supplier for critical components or materials can pose a significant risk. Companies should diversify their supplier base by sourcing from multiple suppliers, preferably in different geographic locations. This strategy mitigates supply chain vulnerability by reducing the dependency on any single supplier and the impact of supplier-related disruptions.
- Multi-Sourcing: Multi-sourcing involves sourcing the same components or materials from multiple suppliers concurrently. This approach ensures that companies have alternative sources of supply readily available in case of disruptions or supply chain constraints from any one supplier.
- Inventory Buffer: Maintaining strategic inventory buffers for critical components, raw materials, or finished goods can help mitigate supply chain disruptions. By holding safety stock or buffer inventory, companies can continue operations even if there are temporary disruptions in the supply of essential items.
- Alternative Transportation Routes: Dependence on a single transportation route or mode (e.g., sea freight, air freight) can increase supply chain vulnerability by exposing supply chains to risks such as port closures, natural disasters, or geopolitical issues. Creating redundancy in transportation by utilizing multiple routes, carriers, or modes of transport can enhance supply chain resilience and ensure continuity in logistics operations.
- Dual Sourcing: Like multi-sourcing, dual sourcing involves partnering with two suppliers for the same component or material. However, in dual sourcing, companies may allocate more of their procurement to one primary supplier while maintaining a secondary supplier as a backup or contingency option.
- Regional Manufacturing Facilities: Establishing regional manufacturing facilities or production lines can provide redundancy in production capabilities. By decentralizing manufacturing operations across different regions, companies can mitigate the impact of localized disruptions, such as natural disasters, political instability, or regulatory changes.
- Supplier Collaboration and Risk Assessment: Close collaboration with suppliers and thorough risk assessments can help identify potential supply chain vulnerabilities. Companies should collaborate with suppliers to implement risk mitigation measures, such as contingency plans, business continuity strategies, and joint monitoring of supply chain performance.
- Advanced Technology and Automation: Leveraging advanced technologies such as artificial intelligence (AI), the Internet of Things (IoT), and predictive analytics can enhance supply chain visibility, agility, and decision-making capabilities. Automating critical processes can reduce lead times, improve efficiency, and minimize disruptions in production and logistics.
- Strategic Partnerships and Alliances: Forming strategic partnerships or alliances with complementary companies or industry peers can provide access to additional resources, expertise, and supply chain capabilities. Collaborative partnerships can facilitate resource sharing, joint risk management, and collective response to supply chain crisis.
- Continuous Monitoring and Scenario Planning: Implementing robust monitoring mechanisms and scenario planning tools enables companies to proactively identify potential disruptions, assess their impact, and develop response strategies. Continuous monitoring of key performance indicators (KPIs), market trends, and geopolitical developments allows for agile decision-making and adaptation.
Conclusion
Implementing these redundancy strategies can help companies create a resilient supply chain that can withstand disruptions and ensure business continuity. Remember, in today’s volatile business environment, redundancy is not an option – it’s a necessity!
It’s important to choose the right technology from a trusted provider to support your supply chain risk mitigation strategies. Infor is a global leader in cloud software solutions built for companies in industry-specific markets, including Distribution. Over 60,000 organizations worldwide rely on Infor to help overcome market disruptions and achieve business-wide digital transformation.
Will Quinn is the Global Director of Product Strategy for Infor. Will boasts 25+ years in supply chain and logistics. Prior to Infor, he managed distribution centers at Grainger, Coca-Cola, MSC Industrial Supply, WEG Electric, and Cintas. Will’s logistics journey commenced with a 12-year tenure in the US Marine Corps. He holds a Master of Science in Supply Chain Management from Elmhurst University.
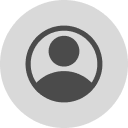
Supply Chain Moves
Supply Chain Moves is a publication dedicated to the supply chain industry, particularly the companies, people and events that help drive global commerce.